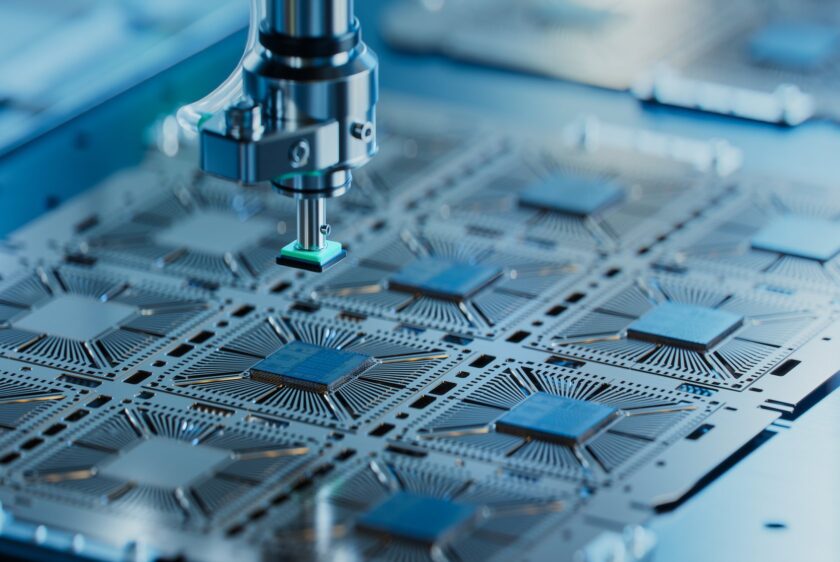
High-Touch Electronics Manufacturing: What Sets a True EMS Partner Apart
In the realm of complex electronics manufacturing—especially within regulated industries such as medical, aerospace, and defense—the stakes are too high to collaborate with a partner who merely follows instructions.
Anyone can accept a BOM and spin up a build. Very few partners can anticipate risk, improve design outcomes, and protect your long-term roadmap.
That is the distinction between a transactional EMS provider and a high-touch EMS partner.
In this article, we break down what sets high-touch electronics manufacturing apart—not just in capabilities, but in mindset, collaboration, and how these partners show up when it matters most.
If you’re building products that can’t afford to fail, here’s what to look for.
What Is High-Touch Electronics Manufacturing?
“High-touch” doesn’t mean high-maintenance.
It means high visibility, high alignment, and high accountability.
It’s a strategic way of working that reduces upstream risk, protects your IP, and helps you launch faster—with fewer surprises, fewer resets, and far more confidence.
A high-touch EMS partner brings:
- Proactive engineering collaboration
- Real-time technical communication
- Process transparency you don’t have to chase
- A build system that flexes without breaking
- A partnership that scales with you—not away from you
1. A Seat at the Table—Not Just a Spot on the Quote List
High-touch EMS partners engage early—before layout is finalized.
They don’t just take orders; they help shape better outcomes.
That means providing:
- Design for Manufacturability (DFM) input
- Test access and fixture strategy (DFT)
- BOM risk and lifecycle analysis
- Thermal and mechanical design feedback
- Compliance implications for FDA, ITAR, ISO, and more
At EST, we routinely join customer design reviews and NPI sessions—because late-stage failure is often rooted in early-stage silence.
2. Traceability Systems Built for High Stakes—Not Just High Volume
In high-touch electronics manufacturing, every unit counts.
Especially when:
- It’s destined for clinical trials
- It’s a one-of-a-kind prototype
- It’s subject to regulatory review
That’s why traceability starts at spin one:
- Unit-level serialization
- Full DHR/DHF documentation
- Operator and test logs
- BOM and firmware version control
- Documented ECO workflows—even on low-volume runs
This isn’t about scale. It’s about precision.
3. Engineers Who Speak “Design” and “Operations”
Most EMS providers assign a coordinator or sales contact. Helpful—until something breaks.
High-touch EMS partners give you direct access to engineers who:
- Understand your application and design intent
- Know what causes rework, scrap, and variability
- Can suggest improvements—not just quote parts
- See around corners before issues harden into defects
These are thought partners—not box-checkers.
4. Class 3 Workmanship—No Special Request Needed
In regulated markets, IPC Class 3 workmanship isn’t optional. It’s table stakes.
At EST, Class 3 is built in:
- Certified operators and inspectors
- Documented processes and verification
- Zero upcharge for the standard your product demands
If your EMS partner waits for you to request quality, you’re already behind.
5. Root Cause Over Finger-Pointing
When things go wrong (and in high-mix manufacturing, they sometimes do), you want a partner who owns the issue—without deflecting blame.
High-touch EMS teams default to investigation, not excuses:
- Pulling operator logs
- Reviewing component history and substitutions
- Running failure analysis
- Updating process controls or DFM feedback
It’s not about who’s “at fault.” It’s about how fast and clearly you solve it—together.
6. Continuity from Prototype Through Production
Handing off between vendors is one of the most dangerous moves in complex builds.
- Your prototype shop won’t scale
- Your production partner won’t take early-stage risk
- Knowledge is lost in translation
High-touch EMS partners close that gap:
- Same core team across all phases
- Test systems evolve—not restart
- Traceability scales
- Materials strategies are proactive—not reactive
At EST, we’ve supported customers from first unit through FDA approval and post-market change control—with zero partner changes.
7. Visibility You Don’t Have to Chase
In high-touch electronics manufacturing, silence is a risk.
Waiting days for a BOM update or change order approval? That’s unacceptable.
What you should expect:
- Dedicated technical program managers
- Shared dashboards or status check-ins
- Transparent scheduling and part lead time updates
- Escalation paths that don’t require escalation
You should never have to ask twice—or guess once.
8. Compliance as a Built-In Discipline—Not a Fire Drill
High-touch EMS partners don’t just hang certificates on the wall. They operationalize compliance.
That means traceability, training, documentation, and audit readiness at every touchpoint.
At EST, we speak fluent:
- ISO 13485
- AS9100
- ITAR
- 21 CFR Part 820
- CE and MDR
We also understand the unspoken expectations of your regulators—because we’ve been through those audits, too.
9. Flexibility Without Fragility
In regulated product development, change is inevitable.
Forecasts shift. Designs evolve. Requirements get updated mid-stream.
High-touch EMS partners don’t panic. They plan:
- Full quality controls on low-volume builds
- Quick-turn ECOs with documentation updates
- Systems that flex without breaking
- Real-time visibility into impacts and path forward
You can’t control volatility. But you can choose a partner built to handle it.
Final Thought: High-Touch EMS Is a Strategic Advantage
High-touch electronics manufacturing isn’t about VIP service. It’s about operational fluency, shared risk, and precision you can trust.
It’s a mindset. A discipline. A way of working that earns confidence—one unit at a time.
If your product will be:
- Implanted
- Launched
- Audited
- Deployed
You don’t just need parts soldered. You need trust built in.