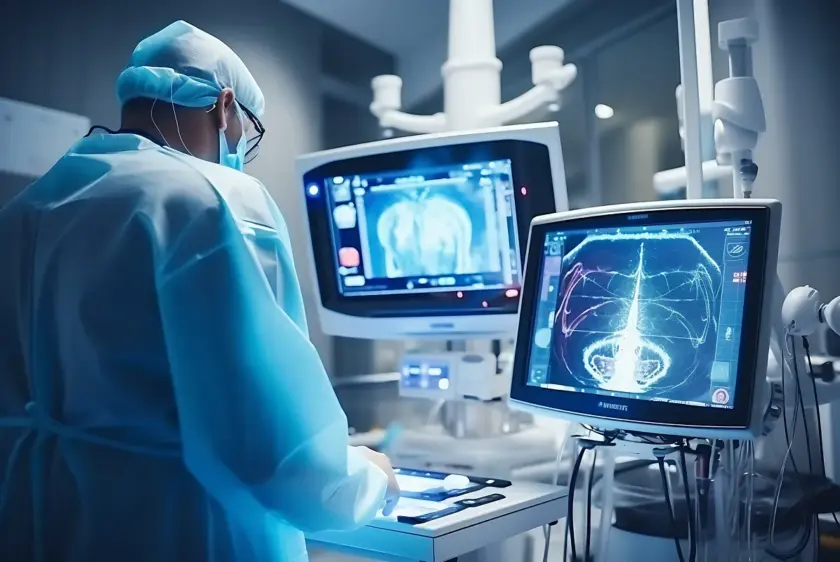
Medical Device Manufacturing: 5 Compliance Mistakes That Cost Millions
For medical device manufacturers, ensuring regulatory compliance isn’t just about following rules—it’s about patient safety, avoiding legal liability, and keeping products on the market. Non-compliance can result in costly product recalls, FDA warnings, and contract losses.
At EST, we specialize in ISO 13485-certified medical device manufacturing, helping companies meet strict regulatory requirements while ensuring quality and traceability. Here are five common compliance mistakes—and how to avoid them.
1. Using a Non-Certified Manufacturer
❌ Mistake: Assuming All Manufacturers Meet Medical Standards
Not all contract manufacturers are ISO 13485-certified or FDA-registered, meaning they may not meet required safety and quality standards.
Example: A startup outsourced PCB assembly for a wearable medical device to an offshore supplier. The manufacturer lacked ISO 13485 compliance, leading to failed audits and an FDA recall.
Solution: Work with a certified medical device manufacturer that meets ISO 13485, FDA, and GMP standards.
EST Advantage: We are ISO 13485-certified, FDA-registered, and specialize in high-reliability medical electronics manufacturing.
2. Lack of Full Traceability & Documentation
❌ Mistake: Incomplete Records Lead to Audit Failures
The FDA and ISO 13485 require that every component, material, and process is fully traceable. Many manufacturers fail to maintain proper documentation, leading to audit failures and product recalls.
Example: A medical device firm failed an FDA inspection because they couldn’t provide full traceability on electronic components used in their PCBs. The result? A product hold that cost $5 million in lost revenue.
Solution: Choose a contract manufacturer that provides full traceability—from supplier sourcing to final product assembly.
EST Advantage: We provide complete documentation, serial tracking, and component traceability to ensure 100% audit readiness.
3. Poor Quality Control & Testing
❌ Mistake: Relying on Minimal Testing
Medical electronics must meet high reliability standards—a failure in the field can result in patient harm or death. Many manufacturers skip advanced testing to cut costs, increasing the risk of product failure.
Example: A company producing portable patient monitors experienced a 12% device failure rate due to poor soldering and lack of functional testing.
Solution: Use advanced testing processes, such as:
- Automated Optical Inspection (AOI) to detect assembly defects
- X-ray analysis for hidden solder joint failures
- Functional & In-Circuit Testing (ICT) to ensure device performance
EST Advantage: We provide 100% inspection, AOI, X-ray, and functional testing to ensure zero-defect manufacturing.
4. Choosing the Wrong Materials or Components
❌ Mistake: Using Non-Biocompatible or Non-Compliant Materials
Many medical electronics require specific materials that meet FDA, RoHS, and ISO 10993 standards. Using the wrong components can lead to regulatory rejection and product recalls.
Example: A medical device manufacturer sourced PCBs with non-RoHS-compliant solder, failing European CE compliance and leading to $3 million in lost sales.
Solution: Work with a contract manufacturer that ensures material compliance and helps with component selection for regulatory approval.
EST Advantage: We source ISO 13485 and RoHS-compliant components and ensure all materials meet medical-grade safety standards.
5. Failing to Consider Scalability & Production Stability
❌ Mistake: Not Planning for Manufacturing Scale-Up
Many medical device companies don’t plan for scaling production from prototype to full-volume manufacturing. Choosing the wrong manufacturer can lead to:
- Inconsistent production quality
- Unstable supply chains
- Delays in regulatory approval
Example: A company developing an implantable neurostimulation device built prototypes overseas—but had to switch to a U.S. manufacturer to meet FDA production stability requirements. The transition delayed their product launch by a year.
Solution: Work with a manufacturer that can support prototyping, low-to-mid volume production, and full-scale manufacturing.
EST Advantage: We provide low-to-mid volume, high-reliability manufacturing with a seamless transition from prototype to full production.
6. The EST Approach to Medical Device Manufacturing Compliance
🔹 ISO 13485-Certified, FDA-Registered Manufacturing We ensure every product meets strict medical device regulatory standards for quality and compliance.
🔹 Full Component Traceability & Compliance Documentation We provide end-to-end tracking and full audit readiness to eliminate regulatory risks.
🔹 Advanced Testing & Quality Control Our AOI, X-ray, and functional testing ensure zero-defect production for mission-critical medical devices.
📌 What this means for you: No audit failures, no compliance risks, just high-quality, fully certified medical device manufacturing.
7. Why Choose EST for Medical Device Manufacturing?
✔ Reduce Compliance Risks with Certified Production We provide ISO 13485, FDA-registered manufacturing for medical devices.
✔ Full Traceability & Documentation for Regulatory Approval We offer 100% component traceability, process validation, and compliance documentation.
✔ Scalable Production from Prototype to Full-Volume Manufacturing We support low-to-mid volume medical device production with full regulatory compliance.
📌 Bottom Line: Don’t risk non-compliance—partner with an ISO 13485-certified manufacturer that guarantees quality and regulatory approval.
Need ISO 13485-Certified Medical Device Manufacturing? Contact EST Today
📞 Call us today at (760) 214-9183
📧 Email us at [email protected]
Compliance matters. Quality saves lives. Let’s build it right the first time.