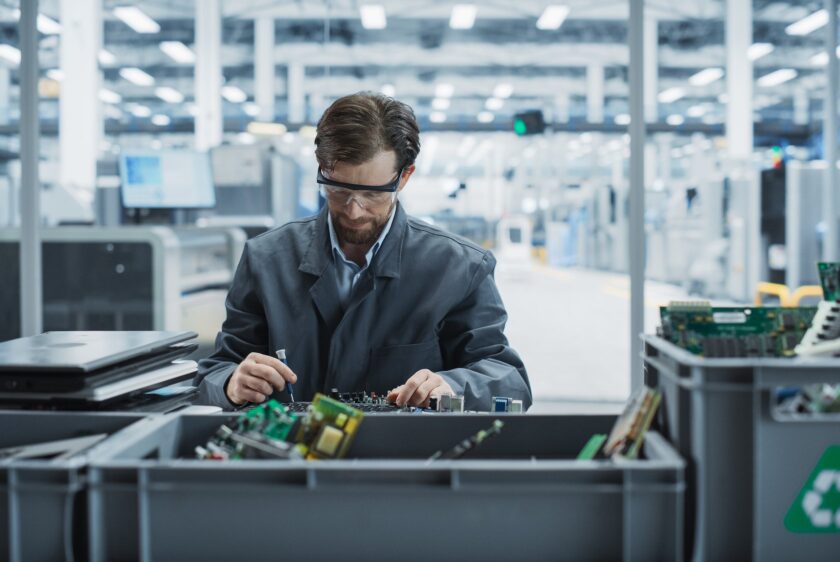
In highly regulated industries like the medical device industry, defense systems, and high-performance industrial controls, quality isn't just about performance; it’s about proof. In the complex realm of electronics manufacturing, few certifications carry more weight than ISO 13485:2016 certification.
ISO 13485 is the global gold standard for quality management systems specific to medical devices and related services. Its scope, however, extends well beyond healthcare. For both OEMs and startups, partnering with an ISO 13485 certified electronics manufacturer provides a trusted foundation for compliance, reliability, and accelerated market access.
More Than a Certificate—A Commitment to Excellence
This article unpacks what ISO 13485 certification really means, why it matters beyond just medical applications, and how EST leverages this discipline to deliver compliant, high-reliability electronics at every stage of development.
What Is ISO 13485?
ISO 13485:2016 is a comprehensive quality management system standard developed specifically for the design, development, production, installation, and servicing of medical devices. It expands on ISO 9001 with stricter requirements for:
- Risk management and mitigation throughout the product lifecycle
- Design control and verification processes
- Regulatory documentation and auditability
- Process validation, traceability, and contamination control
- Supplier controls and corrective/preventive action (CAPA)
Unlike ISO 9001, ISO 13485 emphasizes not just consistency but compliance with applicable regulatory requirements in multiple markets—such as FDA 21 CFR Part 820 in the U.S. and MDR in Europe.
Why ISO 13485 Matters in Electronics Manufacturing
While ISO 13485 was originally designed for the medical device industry, its discipline applies equally to any product where failure is not an option. For electronics manufacturers supporting life-critical, safety-critical, or compliance-sensitive applications, this certification signals more than quality—it signals readiness.
Key industries that benefit from an ISO 13485 certified EMS partner include:
- Medical Devices and Wearables
- Surgical Imaging and Monitoring Equipment
- Defense and Aerospace Electronics
- Industrial IoT with Environmental Safety Requirements
- Diagnostic and Laboratory Equipment
These sectors share a need for traceability, process rigor, and documentation that satisfies both internal stakeholders and external auditors.
What Sets an ISO 13485 Certified Manufacturer Apart
Here are seven core advantages of working with a certified partner like EST:
1. Built-In Regulatory Readiness
ISO 13485-certified systems are structured for full regulatory traceability, including:
- Design History File (DHF) management
- Device Master Record (DMR) and Device History Record (DHR) generation
- Risk mitigation through FMEA and documented verification
- Change control with formalized ECO processes
At EST, we integrate these practices from NPI solutions through final assembly, providing turnkey documentation support for customers preparing for FDA clearance, CE marking, or third-party audits.
2. Process Control and Repeatability
From SMT reflow to functional test, every process step is controlled under ISO 13485-compliant SOPs. Key process validation includes:
- Equipment calibration and maintenance logs
- Operator training and qualification tracking
- Statistical process control (SPC) on critical steps
- Lot-level traceability for components and builds
This ensures product consistency across builds and significantly reduces field failure risks, adhering to the highest quality standards.
3. Full Traceability at the Component Level
Whether a client is shipping Class II medical equipment or sensor arrays into a defense application, traceability is non-negotiable. EST offers:
- Barcoding and serialization at the board and unit level
- Lot-controlled component tracking
- Documented chain-of-custody for materials and subassemblies
- Retained sample protocols and yield tracking
These practices allow for rapid root cause analysis and simplify regulatory reporting.
4. Integrated Risk and CAPA Systems
A mature quality system doesn't just prevent errors—it learns from them. EST’s ISO 13485-certified QMS includes:
- Root cause investigations for every NCR
- Closed-loop CAPA procedures
- Risk analysis integrated with ECO approvals
- Continuous improvement tracking across builds and programs
This feedback loop reduces the likelihood of repeat issues and supports long-term quality improvements.
5. Sourcing Controls and Supplier Qualification
ISO 13485 requires that all suppliers meet predefined qualification criteria. At EST, this includes:
- Approved vendor list (AVL) maintenance
- First-article inspection (FAI) on new materials
- Periodic supplier audits and scorecard reviews
- REACH, RoHS, and conflict mineral declarations
This ensures every component meets environmental and regulatory requirements and that your BOM is built for long-term compliance.
6. Medical-Grade Cleanliness and Environmental Controls
For ISO 13485-compliant builds—especially in MedTech and optical devices—environmental control is critical. EST maintains:
- Controlled assembly zones
- Electrostatic discharge (ESD) safe workstations
- Cleanable surfaces and contamination control protocols
- Temperature and humidity monitoring for sensitive builds
These controls support the safe design of patient-critical and mission-critical systems.
7. Faster Path to Market with Reduced Regulatory Risk
Products built under ISO 13485 systems are more likely to pass audits, qualify for clinical trials, or achieve MDR/FDA submission without delay. That’s because the EMS partner’s records support your regulatory filings with:
- Process validation records
- Full DHR and batch history
- Calibrated inspection results
- Documented operator certifications
By removing compliance uncertainty, EST gives you faster approval, lower cost of rework, and a smoother path to scale.
Case Snapshot: Accelerating FDA Readiness
A VC-backed medical diagnostics company partnered with EST to transition from lab prototypes to audit-ready production. Requirements included:
- ISO 13485 certified processes
- Full unit serialization
- Integrated firmware flashing and validation
- Clean, audit-ready DHR documentation
Within six weeks, EST had transitioned their assembly and test processes to meet submission standards, passed a mock audit, and helped the company achieve 510(k) clearance three months ahead of schedule.
Beyond Compliance: Why ISO 13485 Also Signals Strategic Fit
Working with an ISO 13485 certified electronics manufacturer is not just about ticking a regulatory box. It’s about:
- Building stakeholder trust (especially in investor or enterprise due diligence)
- Aligning with procurement standards of large OEMs or hospital networks
- Enabling smoother transitions into global markets
- Demonstrating systems maturity to insurance, clinical, or defense partners
- Reducing exposure to recalls, rework, and costly audit delays
In short: certification supports commercialization.
What to Ask When Vetting an ISO 13485 EMS Partner
When evaluating electronic manufacturing services for ISO 13485 builds, ask:
- Are your ISO 13485 certifications current and facility-specific?
- Can you provide example DHRs or process validation records?
- Do you support FDA, CE, or MDR submission documentation?
- What environmental controls are in place for medical builds?
- How is risk managed across the production lifecycle?
- Can we audit your electronics manufacturing facility before launch?
If the answers are unclear—or worse, if the documentation doesn’t exist—you may be buying risk instead of reliability.
Why EST
EST has been ISO 13485 certified since 2014 and has supported dozens of medical device startups, diagnostics firms, and compliance-sensitive OEMs through design validation, regulatory review, and commercial scale-up.
Our full suite of certifications includes:
- ISO 9001:2015
- ISO 13485:2016
- FDA Registered
- GMP Compliant
- ITAR Registered
- J-STD-001 and IPC-A-610 Class II and III
Combined with X-ray inspection, AOI, functional test development, and end-to-end traceability, we offer more than just compliant builds—we offer confidence and high-quality products that meet the highest quality standards.
Key Takeaways
- ISO 13485 certification is essential for high-stakes electronics builds—not just for MedTech, but for any application requiring auditability and process discipline.
- Certified EMS partners like EST help de-risk product development, accelerate regulatory approvals, and support scale-up with complete traceability and documentation.
- ISO 13485 is not a feature. It’s a foundation—and when it’s embedded into your manufacturing partner’s DNA, it becomes a growth enabler, not just a requirement.