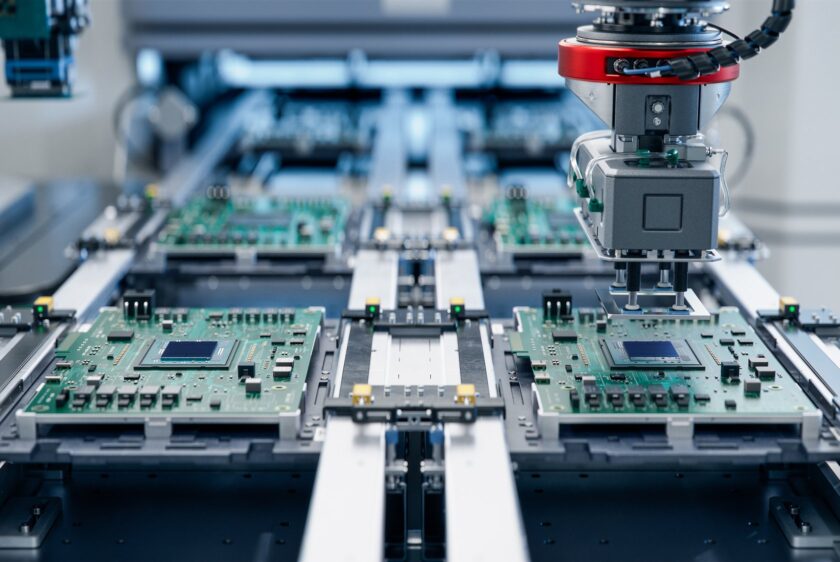
Many engineering teams know the acronym "DFM." It's often mentioned in rushed design reviews and casually claimed as practiced, yet the comprehensive understanding of Design for Manufacturability (DFM) remains elusive. But fully grasping DFM's scope is essential—it can make the difference between smoothly scaling production or getting stuck in costly production delays.
DFM isn't merely about tweaking layouts to improve yield. It involves a strategic mindset where design, sourcing, assembly, and scaling are seen as an interconnected system rather than separate, sequential steps. In complex electronics—particularly medical, aerospace, industrial, or defense sectors—adopting DFM effectively separates successful product iterations from expensive, time-consuming stall-outs.
This glossary entry clarifies what DFM is, what it isn't, and why it must be foundational to your product strategy.
Defining Design for Manufacturability (DFM)
DFM is an engineering approach to product design aimed at simplifying and optimizing manufacturing without compromising performance, safety, or compliance. Effective DFM ensures:
- Consistent, repeatable production
- Cost-efficient assembly processes
- Reliable quality inspection and testing
- Supply chain-compatible sourcing of materials and components
At its core, DFM bridges design intent with real-world manufacturing capabilities.
Why DFM is Crucial for Complex Electronics
In regulated, high-reliability sectors, manufacturability challenges do more than slow down production. They:
- Increase costs and scrap rates
- Disrupt certification timelines
- Introduce risks to field performance
- Create vulnerabilities during audits
- Force last-minute, costly design changes
Engineering teams frequently face "perfect" designs that work in simulations but fail during SMT assembly due to shadowing, skew, or standoff issues. Other teams experience sourcing failures, despite BOMs passing electrical reviews, or encounter assembly nightmares from enclosures designed without practical considerations. DFM proactively addresses these challenges, preventing production hiccups from escalating into broader business issues.
What DFM Covers (And What It Doesn't)
DFM encompasses:
- PCB layout guidelines (pad sizes, clearances, stencil design)
- Component orientation for efficient pick-and-place
- Thermal management solutions (heat sinks, airflow paths)
- Panelization strategies
- Test points and accessibility for in-circuit testing (ICT)
- Mechanical tolerance management
- BOM analysis for availability and lifecycle
- Assembly-friendly connector and cable design
- Compliance with IPC standards (Class 2 or 3)
DFM does NOT include:
- Functional testing or performance verification
- Comprehensive mechanical strength modeling
- RF or signal integrity analysis
- Industrial design aesthetics
DFM intersects but is distinct from Design for Testability (DFT), Design for Assembly (DFA), and Design for Reliability (DFR).
When Should You Implement DFM?
Ideally, DFM should begin at the earliest design phases. Too often, teams treat DFM as a final step before manufacturing—akin to editing a screenplay after filming. Instead, early integration into design decisions such as component selection, board stack-up, power distribution, and enclosure constraints is crucial.
At EST, pre-layout DFM reviews involve collaborative discussions between our manufacturing engineers and the customer's design team. These reviews address high-risk component placements, costly routing paths, assembly barriers, and sourcing constraints. Addressing these issues in CAD is straightforward; identifying them on the production line leads to costly delays.
Common DFM Mistakes (And How to Avoid Them)
- Components too close to board edges/mounting holes
Result: Cracked solder joints, poor automated optical inspection (AOI)
Fix: Observe IPC guidelines, maintain clearances - Using exotic/custom component footprints
Result: Manual placements, reduced yield, slower cycles
Fix: Use standard, IPC-compliant packages - Overcrowded layouts lacking thermal relief
Result: Warping, reliability issues
Fix: Design with adequate thermal management space - Omitting test points
Result: Limited troubleshooting, incomplete functional testing
Fix: Include accessible test points and headers - Specifying long lead-time components
Result: Delays, compliance issues
Fix: Early availability checks, qualify alternates proactively
DFM in Regulated Industries
For sectors like medical (ISO 13485), aerospace (AS9100), defense (ITAR/EAR), industrial automation, and energy (UL/IEC standards), DFM isn't optional—it's a compliance requirement. Your EMS partner should fluently integrate regulatory and engineering expertise.
How EST Implements DFM
At EST, DFM is integral—embedded in quoting, production, and advising. Our proactive DFM reviews, robust test strategies, and thorough BOM screenings ensure manufacturing readiness. Post-production feedback from the floor continually refines designs and reduces total quality costs.
The Business Case for DFM
Properly executed DFM delivers tangible benefits:
- Higher first-pass yields
- Lower production costs
- Accelerated ramp-up
- Improved audit performance
- Enhanced product reliability
- Streamlined regulatory approvals
- Reduced late-stage redesigns
- Faster market entry
For engineers and product owners focused on performance, safety, and cost, DFM integrates these priorities seamlessly. At EST, we ensure every design choice strengthens your product’s manufacturability, reliability, and scalability.
Ready to review your design through a DFM lens? EST can pinpoint risks early, saving you costly delays. Let’s talk.