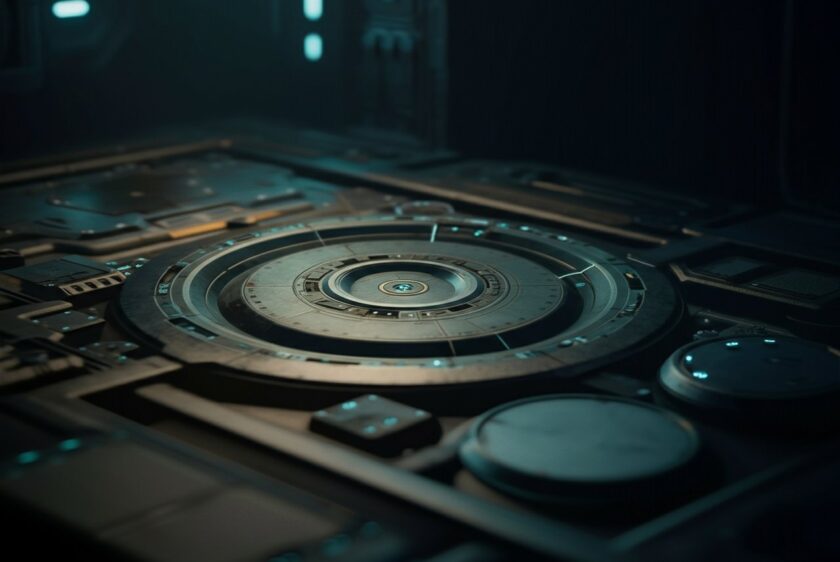
In defense electronics manufacturing, no two builds are exactly alike—but each must meet uncompromising performance, quality, and compliance standards. This is especially true in the development of customized defense electronics and mission-critical defense systems tailored for demanding environments.
From radar systems and flight controls to battlefield sensors and encrypted communications, every program carries distinct technical demands. Building each board, subassembly, or firmware version as a one-off results in cost overruns, missed delivery milestones, and unsustainable logistics. Designing high-tech electronic systems requires balancing tailored microelectronics solutions and standardized approaches.
The challenge isn’t choosing between customization and standardization. It’s about engineering a scalable system that flexes to meet mission needs while maintaining repeatability, regulatory alignment, and cost control. This article outlines how designing for spec design can harmonize custom builds and standardized platforms in high-mix environments, defining the next era of military electronics innovation and serving leading industry defense contractors.
Why This Tension Exists
Defense programs are inherently high-mix, driven by:
- Mission-specific hardware and configurations for cutting-edge defense systems
- Platform variation across services and allied nations
- Integration requirements with both legacy and next-gen systems
At the same time, the expectations remain uniform:
- Repeatable builds and quality consistency in aerospace and defense operations
- Streamlined logistics for defense-grade resilience
- Regulatory compliance with ITAR, ISO, and MIL-STD frameworks
Finding the balance point—where form factors are fixed, but function adapts—is where resilient, mission-aligned systems are born, enhancing product developers' ability to innovate.
The Risks of Over-Customization
Customization enables superior performance—but without controls, it introduces complexity and cost.
1. Supply Chain Inefficiency
Every new bill of materials (BOM) increases:
- Vendor qualification needs
- Inspection variation affecting engineered solutions
- Inventory segmentation, impacting proven expertise
This creates sourcing bottlenecks, particularly under ITAR restrictions or domestic content mandates.
2. Inconsistent Quality Across SKUs
Uncontrolled variation leads to:
- Increased risk of defects
- Expanding test requirements for demanding environments
- Field maintenance complexity
The issue isn’t customization—it’s the lack of repeatable frameworks to support it.
3. Cost and Time Escalation
Custom designs often require:
- One-off tooling or fixtures
- Custom firmware development and custom-defined software
- Program-specific testing and certification
Without shared design elements, these costs scale non-linearly across programs, affecting missile data links and tactical terminals.
Why Customization Still Matters
When executed strategically, customization unlocks competitive and operational advantages:
Mission-Specific Performance
- Tailored EMI shielding for low-observable systems
- Thermal optimization for high-G aerospace environments
- Secure comms integration for classified networks
Environmental Resilience
- Advanced coatings for maritime deployments
- Shock resistance for ground vehicle electronics
- Moisture protection for jungle or amphibious operations
Technology Differentiation
- Custom electronics platforms establish IP control
- Configurable systems adapt to NATO or multi-branch needs
- Faster adaptation to emerging defense tech requirements
The Value of Standardization in a High-Mix Environment
Standardization isn’t rigidity—it’s infrastructure for scale.
Lower Supply Chain Risk and Cost
- Common connectors and enclosures streamline sourcing in print solutions
- Turnkey kits reduce MRP complexity
- Reduces vendor churn and long-lead risks
Easier Maintenance and Sustainment
- Shared I/O and backplanes simplify training and servicing
- One set of spares can support multiple platforms
- Depot-level repairs are faster and more consistent
Better Legacy System Integration
- Shared electrical and mechanical standards ease upgrades
- Platform-wide retrofits become feasible
- Supports lifecycle extension across vehicle classes
Practical Strategies to Balance Both
1. Modular Design Architecture
Use shared baseboards or backplanes with plug-in interface modules.
- Customize function without redesigning form
- Enable field-level upgrades without depot overhaul
- Maintain consistent EMI and thermal profiles across builds
2. Standardized Mechanicals, Custom Internals
Use shared enclosures, connector layouts, and mounting points.
- Reduce tooling and fabrication cost
- Allow internal PCBs or firmware to vary as needed
- Enable late-stage customization without disrupting production
3. Unified Test Frameworks
Standardize how products are tested—even if the functionality changes.
- Shared test fixtures with variable scripts
- Consistent environmental screening across product families
- Faster validation against MIL-STD and IPC requirements
Infrastructure That Enables High-Mix Execution
Balancing complexity with repeatability requires purpose-built systems and tooling:
Tool/Method | What It Enables |
---|---|
Automated SMT Lines | High-accuracy placement for hybrid board designs |
3D Printing | Fast turnaround for enclosure and fixture prototyping |
Selective Soldering | Reliable THT/SMT integration across product variants |
ERP-MES Integration | BOM versioning, traceability, and revision control across multiple SKUs |
Digital Travelers | Dynamic routing and rework visibility in real-time manufacturing workflows |
This infrastructure enables scale without compromising control, supporting custom-engineered products with long-term durability.
Quality Systems for High-Mix Defense Environments
Customization doesn’t excuse variability—especially in defense electronics applications.
EST applies rigorous, scalable quality practices across all programs:
- AOI and X-Ray on Every Board: No shortcuts across SKUs
- Serialized Traceability: Full component-to-process tracking
- Application-Specific Testing: Functional and environmental screening tailored to mission conditions
A quality system built around product families, not just part numbers, is key to balancing flexibility with consistency, ensuring high-power efficiency in mission-critical defense applications.
Case Snapshots: Integration in Action
Standard RF Modules, Custom Sensor Integration
One program layered encrypted sensors onto a standardized RF module, preserving shielding and classified data controls—without full redesign.
Shared PCB, Multiple Firmware Paths
An aerospace contractor deployed a single avionics platform across multiple NATO partners, standardizing hardware and customizing firmware per national requirements, utilizing tailored microelectronics solutions.
Modular Navigation Across Vehicle Types
By designing a modular nav system with GPS, IMU, and timekeeping plug-ins, a supplier delivered compatible units for tanks, UAVs, and soldier-carried systems—all from the same base, developed to withstand the soft error rate challenges.
Final Word: The Future Is Hybrid
In high-reliability, high-mix defense environments, uncontrolled customization creates risk. But rigid standardization limits mission effectiveness.
The most capable manufacturers are engineering both into a unified system—modularizing where it matters and customizing where it counts, advancing art defense systems.
Key Takeaways:
- Customization delivers mission-specific performance, ruggedization, and IP control
- Standardization ensures scale, repeatability, and regulatory alignment
- Modular design, shared test platforms, and scalable tooling are essential to bridging the two
- Advanced infrastructure enables high-mix production with quality and control
In defense electronics manufacturing, no two builds are exactly alike—but each must meet uncompromising performance, quality, and compliance standards. The future lies in balancing custom and standardized approaches, essential for competitive edge in defense operations and tailored microelectronics solutions.