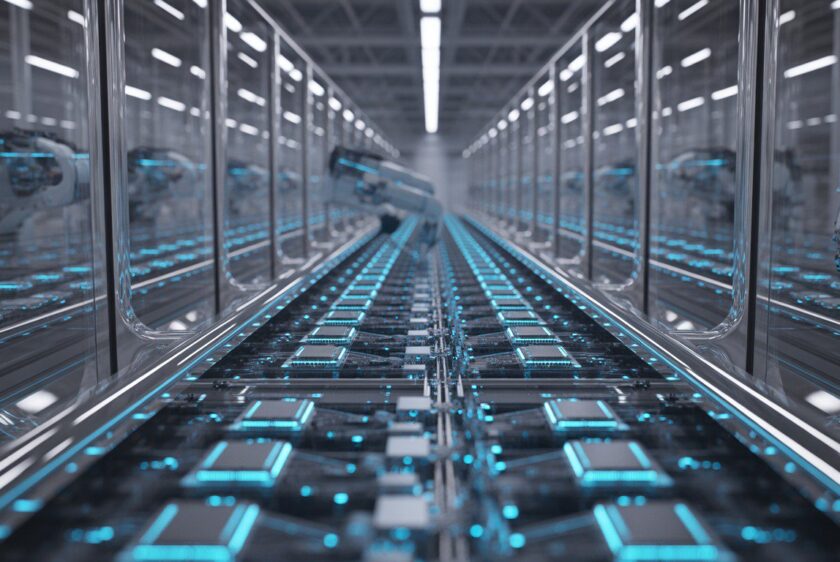
In aerospace, medical, and electronic products manufacturing, achieving full traceability from prototype to production isn't merely beneficial—it's essential. Traceability ensures compliance with stringent regulations, maintains high-quality standards, and safeguards against critical failures. This guide details step-by-step how to implement comprehensive traceability practices aligned with regulatory requirements, industry best practices, and supplier quality improvements.
Step 1: Understand Regulatory Requirements
Before implementing traceability, clearly understand relevant regulations and standards that your industry mandates, especially for OEMs and electronic products manufacturers.
Key Regulations:
- ISO 13485: Critical for medical device manufacturing, it emphasizes traceability throughout the product lifecycle.
- ITAR (International Traffic in Arms Regulations): Essential for aerospace and defense sectors, ensuring secure, compliant handling of sensitive components and technologies.
- FDA Compliance: Mandates thorough documentation and traceability for medical devices, ensuring patient safety and product reliability.
Step 2: Define Your Traceability Strategy
Establish a robust traceability strategy encompassing component identification, tracking methods, and documentation standards to maintain high supplier quality.
Critical Elements:
- Component-Level Traceability: Each component must have unique identifiers, allowing precise tracking through the manufacturing lifecycle, such as serial numbers.
- Digital Documentation: Implement systems to digitally document the history of each component, including specific production batch information, production stages, and inspection results for raw materials.
Step 3: Implement Unique Identification Methods
Effective traceability begins with accurately identifying components through reliable, standardized methods, crucial for electronics manufacturers.
Recommended Technologies:
- Barcoding: Utilize barcode labels for easy scanning, providing quick access to component data and enabling visibility.
- RFID Tags: Allow wireless tracking and data capture, ideal for complex assemblies in aerospace and medical sectors.
- Serialization: Assign unique serial numbers to each product or batch for accurate tracking throughout the supply chain and ensuring authenticity.
Step 4: Establish Comprehensive Documentation
Rigorous documentation at every production stage is essential for maintaining traceability and compliance with detailed inspection data.
Essential Documentation:
- Process Logs: Document each manufacturing process step, including machinery settings, personnel, and timestamps.
- Material Traceability Reports: Track the origin, handling, and integration of raw materials into the finished product.
- Inspection Records: Maintain thorough records from quality control processes like Automatic Optical Inspection (AOI) and X-Ray analysis, ensuring defect-free components and adherence to industry standards.
Step 5: Integrate Traceability Early in Prototyping
Integrating traceability from the prototype stage significantly enhances overall process effectiveness, including PCB assembly quality control.
Action Items:
- Design Reviews: Include traceability as a critical criterion in design-for-manufacturability (DFM) reviews.
- Prototyping Logs: Maintain detailed records during prototyping, documenting design changes and iterations clearly, utilizing IPC-1782 standards as a guide.
Step 6: Scale Traceability for Production
Transitioning from prototyping to full-scale production requires consistent traceability practices and strict adherence to established protocols, including EMS manufacturing.
Operational Steps:
- Develop Standard Operating Procedures (SOPs): Define clear, consistent procedures for traceability, from initial receipt of components to final product delivery.
- Implement Automated Systems: Leverage automated processing machines and traceability software systems to ensure accuracy, efficiency, and repeatability with high-quality parts.
Step 7: Utilize Advanced Inspection and Testing
Incorporating advanced quality control technologies helps ensure traceability and product reliability, fostering consumer trust.
Recommended Inspection Methods:
- Automatic Optical Inspection (AOI): Detects surface defects and verifies component placement automatically.
- X-Ray Analysis: Non-destructive testing of internal components, critical for aerospace and medical electronics, ensuring hidden defects are identified early.
Step 8: Continuous Improvement & Regular Audits
Ensure ongoing compliance and enhance traceability systems through continuous improvement processes and regular audits.
Continuous Improvement Practices:
- Regular Audits: Conduct internal and external audits to validate adherence to ISO, FDA, and ITAR regulations.
- Process Optimization: Continuously refine traceability processes based on audit findings and operational feedback to meet regulatory requirements effectively.
Benefits of Robust Traceability
Adopting these traceability practices yields significant operational benefits:
- Enhanced Quality Assurance: Proactive identification and rectification of defects reduce risk of recalls.
- Streamlined Regulatory Audits: Comprehensive records simplify and expedite regulatory compliance checks.
- Rapid Issue Response: Quick identification and mitigation of product defects protect brand reputation and ensure operational continuity.
Conclusion
In mission-critical industries like aerospace, medical, and electronic product manufacturing, effective traceability from prototyping through production is indispensable. By adhering to stringent regulatory standards, utilizing advanced tracking technologies, and maintaining rigorous documentation practices, manufacturers can significantly enhance product reliability, ensure compliance, and build long-term trust with clients.
Implement these steps consistently to position your organization as a trusted, compliant partner in high-stakes manufacturing sectors, improving integrity and consumer trust in the process.