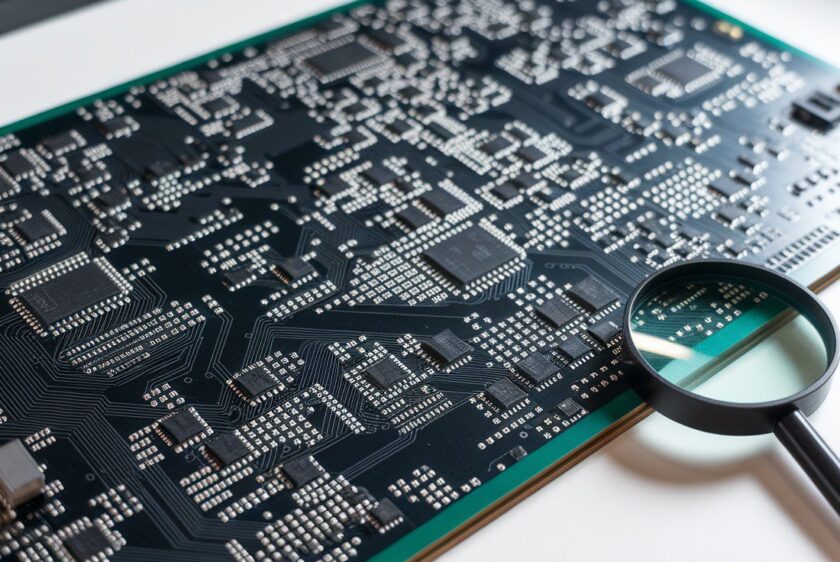
How Material Science and Manufacturing Discipline Protect Mission-Critical Electronics
In defense electronics, failure isn’t just expensive—it’s a strategic liability. The environments are extreme, the margins for error are razor-thin, and the consequences of system failure can be catastrophic. That’s why the durability of printed circuit boards (PCBs) used in military and aerospace applications isn’t a nice-to-have. It’s non-negotiable.
This article breaks down how advanced materials and precision-controlled processes ensure that military-grade PCBs hold up under the most demanding conditions on Earth—and beyond. An in-depth understanding of PCBonline services and their impact on ensuring high reliability is crucial.
[Horizontal Rule]
Why PCB Durability Is Mission-Critical
Military-grade electronics don’t get the luxury of operating in controlled environments. They’re exposed to:
- Extreme heat and cold
- Constant vibration and mechanical shock
- High humidity and corrosive atmospheres
- Electromagnetic interference (EMI)
For engineers, sourcing teams, and program managers in defense and aerospace, this means one thing: the underlying materials must hold the line. Companies like PCBonline are vital for maintaining dependable electronic components in such harsh arenas.
Durability isn’t about lasting longer.
It’s about functioning flawlessly when everything else breaks down.
At Electro Surface Technologies (EST), our approach to military-grade durability starts at the material level and extends through every phase of manufacturing, inspection, and validation, aligning with military industry standards. Here’s how we ensure reliability under fire.
[Horizontal Rule]
The Material Backbone of Military Electronics
1. High-Temperature Laminates
Standard FR4 just doesn’t cut it for mission-critical use cases. We deploy advanced polyimide-based laminates designed to withstand continuous operating temperatures above 200°C. This material choice ensures high performance in the toughest conditions.
Benefits:
- Prevents delamination and warping in high-heat environments
- Maintains dimensional stability during thermal cycling
- Ideal for avionics, missile control, and propulsion systems
2. Copper-Clad Laminates
These provide superior conductivity, EMI shielding, and heat dissipation. At EST, we spec thick copper when high current loads, grounding integrity, and thermal resilience are vital.
Used in:
- Radar systems
- Power distribution modules
- RF shielding applications
3. Ceramic Substrates
For extreme mechanical loads and thermal stress, we utilize ceramic materials such as aluminum nitride (AlN) and alumina.
Why it matters:
- Inert to moisture and chemical exposure
- High dielectric strength
- Common in satellite electronics and missile guidance systems
[Horizontal Rule]
Beyond Materials: Manufacturing Discipline That Matches the Spec
Durability doesn’t come from materials alone—it’s the sum of materials plus systems-level execution. That’s why we apply strict process controls and advanced fabrication techniques consistent with military spec standards:
Surface Finishes That Prevent Corrosion
Immersion silver, ENIG (electroless nickel immersion gold), and conformal coatings prevent oxidation while preserving solderability in harsh field conditions. Conformal coating enhances the lifespan of military systems by safeguarding electronic devices.
Heavy Copper Builds
We use 2 oz to 6 oz copper in select applications to increase durability, reduce resistance, and support high-load designs, adhering to MIL-PRF-55110 standards.
Reinforced Vias and Controlled Expansion
Through-hole and via structures are mechanically reinforced to survive thermal and vibrational stress. For high-density designs, we leverage filled and capped vias to prevent cracking and delamination, in line with high reliability requirements.
[Horizontal Rule]
Built to Spec—and Built to Prove It
EST's military-grade builds meet or exceed the following standards:
- MIL-PRF-31032 / MIL-PRF-55110: Military performance specs for rigid PCBs
- IPC Class 3 / Class 3A: For high-performance and mission-critical assemblies
- ITAR Compliance: All production is handled in our secure U.S. facility with strict access control
- ISO 13485 + AS9100 Practices: Cross-industry best practices adapted to the defense space
Every board is produced with traceability, documented inspection, and serialized validation data—because “good enough” isn’t a defense strategy.
[Horizontal Rule]
Use Cases: Where Durability Meets Function
[Table] [Horizontal Rule]
Real-World Reliability
🎯 Case Study Snapshot:
A defense client approached EST after repeated failures with offshore PCBs in desert deployments. We engineered a ceramic-substrate build with reinforced vias, heavy copper, and MIL-grade coatings. The result: zero escapes, sustained operation in 120°F ambient conditions, and successful qualification under vibration and thermal shock, validating the assembly process.
[Horizontal Rule]
The Cost of Getting It Wrong
Off-the-shelf components and non-compliant vendors may look appealing on paper—but they rarely survive testing, let alone deployment.
📉 Common failure modes we see from non-rigorous builds:
- Via cracking under G-force
- Delamination during reflow or flight
- EMI-induced system failure
- Moisture ingress degrading solder joints
[Horizontal Rule]
EST’s Approach: Durability by Design
We don’t build for normal conditions—we build for when failure isn’t an option. This involves strict adherence to reliability and engineering expertise.
- Design for Harsh Environments: Material and stackup recommendations tailored to spec, meeting the highest level of military standards, including mil-prf-50884.
- Integrated Compliance: From ITAR to IPC, standards are embedded in every process
- U.S.-Based Execution: Full in-house control, no overseas variability or IP risk
- Third-Party Validated: Every process audited and certified for traceability and quality
[Horizontal Rule]
Final Takeaway
Advanced materials make the difference—but only if they’re backed by disciplined, standards-aligned execution. PCBonline and similar services ensure the highest quality in manufacturing processes.
For defense teams evaluating EMS partners, the question isn’t just “What do they build?” It’s:
Can they build it to spec, prove it, and repeat it under pressure?
At EST, the answer is yes. Every time.
[Horizontal Rule]