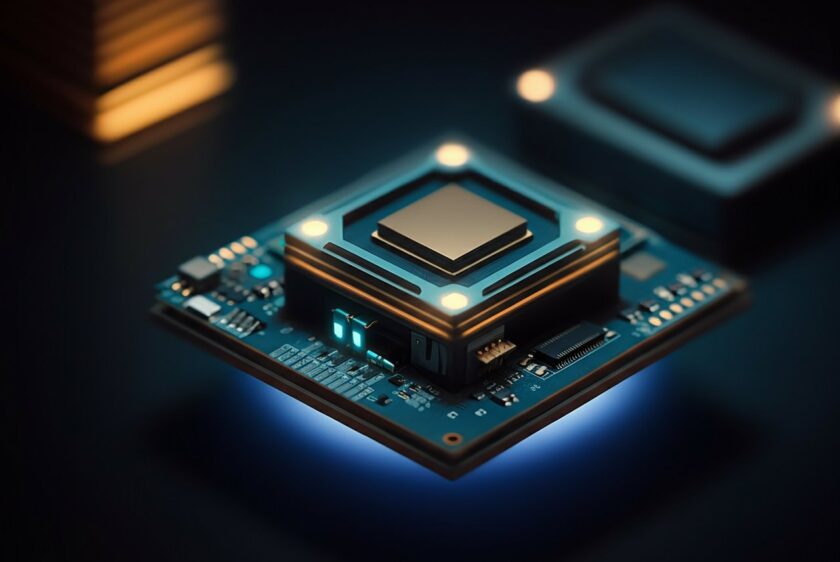
In complex electronics manufacturing, innovation gets the headlines—but compliance gets you to market efficiently and sustainably. Industries like aerospace, medical, energy, and defense are characterized not just by the complexity of engineered products they create, but also by the manufacturing operations and engineered changes they implement. As products become more interconnected and intelligent, compliance becomes a critical part of the entire product lifecycle, rather than a simple back-office task. It is a cross-functional competency essential for manufacturing companies.
For product owners, engineering leads, and startup teams, regulatory maturity within manufacturing operations is about more than just avoiding fines. It's about moving faster with simple manufacturing software, mitigating risks in the various subassemblies and complex products, and building trust with partners, customers, and shop-floor supervisors.
What Compliance Means in High-Stakes Electronics
Compliance is not just about passing a test in discrete manufacturing industries. In highly regulated environments, compliance requires a comprehensive management of:
- Design traceability and engineering changes
- Ensuring electrical and mechanical safety
- Environmental regulations compliance
- Cybersecurity protocols and data protection
- Quality management to ensure high levels of performance
- Supply chain transparency and documentation readiness
As standards evolve and audit expectations grow, reinforced by high levels of quality management, complex discrete manufacturers understand that compliance is a system to build, not just a box to checkIn the realm of complex electronics manufacturing, innovation often captures attention—yet compliance is what actually delivers products to market.
From aerospace and medical to energy and defense sectors, these high-reliability areas are characterized not just by the engineered products themselves, but by how they are manufactured and the proof of compliance provided. As products grow more interconnected, intelligent, and regulated, compliance shifts from being a back-office task to a cross-functional competency essential for manufacturing operations management.
For product owners, engineering leads, and startup teams, reaching regulatory maturity goes beyond avoiding fines. It involves accelerating processes, mitigating risks early, and fostering trust with partners, regulators, and customers.
What Compliance Means in High-Stakes Electronics
Compliance transcends merely passing a test.
In regulated environments, managing compliance involves:
- Design traceability (FDA 21 CFR Part 820, ISO 13485)
- Electrical and mechanical safety (UL, IEC, MIL-STD)
- Environmental regulations (RoHS, REACH, WEEE)
- Cybersecurity protocols (NIST 800-171, ITAR, ISO 27001)
- Quality management (ISO 9001, AS9100, GMP)
- Supply chain transparency and documentation readiness
As standards and audit expectations evolve, the need for robust compliance systems relevant to engineered products becomes a necessity.
Five Realities of Compliance in Complex Electronics
1. Compliance Begins at Design
Compliance kicks off right from the design phase. Regulatory frameworks necessitate:
- User needs linked to design inputs
- Risk analysis and mitigation tracking
- Verification and validation of design outputs
- Traceable engineering changes and process justification
Design History Files (DHF), Failure Mode and Effects Analysis (FMEA), and Verification & Validation (V&V) are integral early on.
2. Documentation Is Part of the Product
In regulated manufacturing, thorough documentation is crucial. Audit-ready records must accompany:
- Bills of Materials (BOMs) with vendor traceability
- Firmware versioning and test outcomes
- Inspection reports tied to serialization
- Engineering Change Orders (ECOs), CAPA, and NCR tracking
3. Your Supply Chain Is a Compliance Variable
Compliance depends on the entire supply chain. Risks include:
- Non-compliance with material requirements (RoHS, REACH)
- Unverified vendors or labs
- Inadequate lifecycle and part tracking
- Outdated certificates
Every BOM should undergo a sourcing risk assessment to flag possible issues.
4. Functional Testing Alone Is Not Enough
General engineering tests are insufficient. Compliance validation covers:
- Repeatability and resilience
- Fault behavior and edge case safety
- System-level integration
Certification-aligned validation and verification plans help evade late-stage failures.
5. Compliance Must Be Cross-Functional
The risk of cultural gaps in compliance is high if it's not a shared responsibility. Roles include:
- Engineering tracking design decisions
- Procurement vetting suppliers and documentation
- Quality managing process and resolution
- Leadership supporting compliance systems
Viewing compliance as an integral discipline increases access and growth potential.
The Compliance Stack
To nurture regulatory maturity, visibility across the product lifecycle is vital:
Layer | Focus | Examples |
---|---|---|
Design Controls | Traceability, risk, inputs/outputs | ISO 13485, FDA 21 CFR 820 |
Supplier Risk | Sourcing and logistics | Vendor audits, AVL tracking |
Process Control | Repeatability and yield | ISO 9001, AS9100, IPC-A-610 |
Cybersecurity & IP | Data security | ITAR, NIST 800-171, ISO 27001 |
Documentation | Change control | DHR, DHF, ECO logs |
Certification | Regulatory filings | UL, CE, FCC, FDA 510(k) |
Strong structural systems enhance scalability and credibility.
Practical Strategies for Compliance-Driven Teams
1. Build a Compliance Map
Identify applicable standards and map them to roles and processes. This collaborative matrix aligns engineering, quality, and operations.
2. Start Pre-Compliance Testing During Prototyping
Early testing of prototypes for safety and emissions reduces delays and costs, ensuring greater compliance at advanced stages.
3. Design for Traceability
Implement hardware and firmware version control. Assign serial numbers and rigorously document each iteration.
4. Choose a Manufacturing Partner Who Supports Compliance
Select EMS partners with certifications like ISO 13485 and real-time traceability infrastructure.
5. Review and Update Compliance Systems Regularly
Conduct quarterly reviews of testing protocols, supplier certifications, and documentation to maintain audit readiness.
Final Thought: Compliance Is a Catalyst for Credibility
Compliance is a pivotal trust engine, demonstrating system maturity to regulators, inspiring customer confidence, and showcasing scalable operations to investors.
At EST, we assist teams in operationalizing compliance as a strategy for market success, ensuring robust manufacturing operations and producing high-quality engineered products.
Key Takeaways
- Regulatory compliance is a system, not a checklist
- Traceability, risk mitigation, and documentation must begin at design
- Supplier and process control are critical to audit-readiness
- EMS partners should provide infrastructure for real-time compliance
- Teams that treat compliance as a shared responsibility scale faster and with less risk