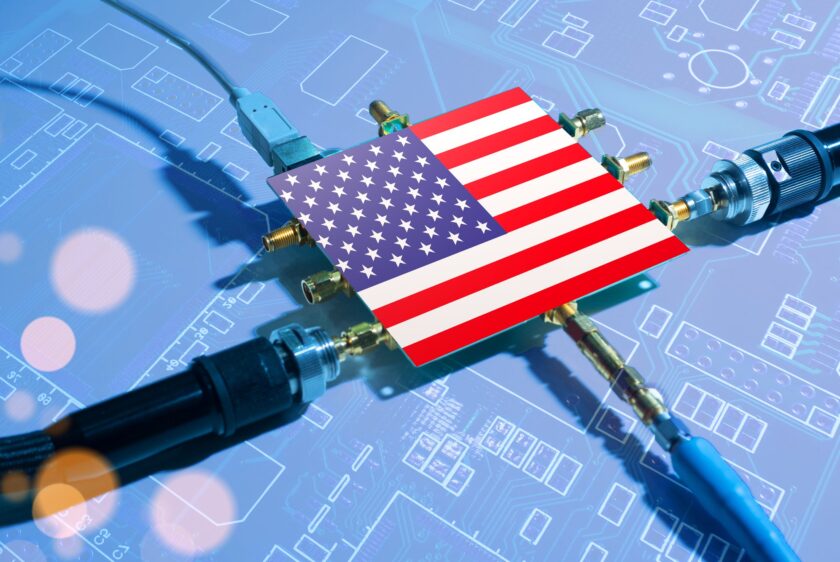
In electronics manufacturing, quality isn’t just a deliverable—it’s a liability line, a regulatory requirement, a brand differentiator, and a gatekeeper to growth. The production process must reflect these priorities to ensure success.
However, when manufacturing operations are outsourced, particularly to offshoring locations, quality control often becomes a black box. Test protocols vary, documentation is inconsistent, and visibility into the line disappears. When issues arise, root cause analysis turns into a time zone-chasing exercise with high stakes for both finances and reputation.
For companies in regulated, high-mix industries like medical devices, aerospace, industrial IoT, and defense, this lack of control isn't sustainable. Reshoring electronics manufacturing—bringing production back to the United States—focuses on building a transparent, proactive quality control infrastructure that scales with complexity, rather than working against it. This shift is critical especially after the covid-19 pandemic highlighted global supply chain disruptions and increasing costs.
Here's how a domestic EMS partner strengthens quality assurance across every layer of your product lifecycle—and why it’s becoming a strategic imperative for high-reliability programs.
The Problem with Offshore Quality Control
Offshore EMS vendors are often chosen for their perceived cost advantages. However, for complex, low-to-mid-volume builds, those short-term savings frequently erode because of gaps in quality oversight, often leading to significant risk mitigation challenges.
- Inconsistent Test Protocols: You may send a test plan, but its application on the floor is another story. Is it followed to spec? Who verifies that the fixture is calibrated? Are failures logged or quietly reworked and pushed downstream?
- Limited Traceability: Many offshore EMS providers operate at a batch level. You might know which lot a unit came from, but not which operator built it, what revision was flashed, or which test stations it passed through. This makes root cause analysis mere guesswork.
- Delayed Access to Critical Data: Without real-time access to yield trends, test logs, or defect reports, quality issues aren’t discovered until it's too late. You don’t know where the issue started—only where it showed up.
- BOM Substitutions Without Visibility: Substituting components for availability reasons is common. However, even small changes in passive components can impact EMI performance, signal stability, or thermal margin. These decisions—when made without transparency—carry significant risk.
For companies that must comply with FDA 21 CFR 820, ISO 13485, ITAR, or MIL-STD protocols, these quality gaps aren’t just frustrating; they’re potentially catastrophic.
How Reshoring Improves Quality Control Across the Lifecycle
Working with a U.S.-based EMS partner offers structural, cultural, and operational advantages that elevate quality control from reactive to strategic. Companies gain greater control and precision in manufacturing, critical for handling changing demands and meeting intellectual property protection standards.
1. Real-Time Visibility You Can Act On
One of the most immediate benefits of reshoring is the enhanced transparency provided by domestic EMS partners like EST. This includes:
- Production dashboards with real-time yield and failure data
- Direct access to quality and process engineers
- In-person audit access and on-site collaboration opportunities
- Immediate alerts on deviations, part shortages, and rework activity
This level of visibility shortens design validation cycles, improves first article review outcomes, and accelerates issue resolution.
Example: An EST client reduced field failures by 48% after reshoring, driven by real-time process feedback during NPI validation builds.
2. Standardized, Auditable Quality Systems
U.S.-based EMS providers operate under stringent quality systems. At EST, this includes:
- ISO 9001 and ISO 13485 certification
- Full ITAR compliance with secure facility protocols
- Operator training certification and continuous competency logs
- Routine internal audits, NCR tracking, and CAPA systems
- Serialized product traceability built into MES from day one
These systems deliver repeatability and build trust into every batch, board, and subassembly, crucial for resolving quality control issues.
3. Accelerated Root Cause Analysis and Continuous Improvement
In a high-mix, low-volume environment, root cause agility is critical. Reshoring enables:
- Shared access to inspection records, soldering profiles, and failure logs
- Face-to-face collaboration between engineering and manufacturing teams
- On-site design-for-testability (DFT) and design-for-manufacturability (DFM) reviews
- Rapid implementation of process or test fixture changes based on live data
This feedback loop—fueled by transparency—reduces failure recurrence and strengthens every next revision.
4. BOM Integrity and Controlled Sourcing
Component substitution is one of the most common offshore failure vectors. A domestic EMS partner mitigates this by:
- Sourcing through authorized, traceable channels
- Enforcing client approval processes for alternates
- Performing incoming inspection with lot validation
- Integrating anti-counterfeit protocols at receiving
With BOMs tied directly to each serialized unit, field failure investigations no longer end in ambiguity.
5. Embedded Firmware Validation and Closed-Loop Testing
In modern electronics, electronics production processes highlight firmware as crucial as solder joints. Reshoring enables:
- Secure, verified firmware flashing by revision and serial number
- In-house functional test development tied to hardware specs
- Joint debugging sessions between client and EMS engineering teams
- Version control tied to MES and QA systems
6. Built-In Compliance and Audit Support
For companies building in regulated sectors, audit readiness is non-negotiable. Domestic EMS partners simplify:
- FDA 21 CFR Part 820 inspections
- ISO 13485 audits and surveillance
- ITAR documentation and physical security compliance
- Customer-driven audits and QMS walkthroughs
At EST, audit preparation is continuous—not a scramble. All documentation is centralized, validated, and exportable.
7. Faster Feedback Loops for Prototypes and Change Orders
For companies launching new products or rapidly iterating, speed is quality. Reshoring unlocks:
- Same-day first article issue review
- ECOs implemented within 48–72 hours
- On-site functional test validation
- Real-time design and yield feedback
This agility allows engineering teams to shift from reactive to proactive quality control—ensuring compliance and reducing the risk of missing production deadlines.
The Real Cost of Poor Quality: Offshore vs Onshore
Poor quality isn’t just a yield issue—it’s a compound cost that shows up in:
Hidden Cost | Offshore Risk | Reshoring Advantage |
---|---|---|
Field failures & RMAs | High (delayed RCA) | Lower (faster feedback) |
Compliance delays | High (doc gaps) | Lower (audit-ready systems) |
Rework & scrap | Hidden | Transparent, controlled |
Customer trust | Vulnerable | Strengthened via visibility |
Timeline slips | Common | Reduced via agile iterations |
When the true cost of quality includes delays, compliance risk, and rework, reshoring becomes a margin-protecting move—not a cost increase.
Case Study: Reshoring in Medical IoT
Background: A medical IoT company outsourced PCBAs to overseas suppliers in Asia. Initial units passed basic test coverage, but 12% of units failed in the field within six months.
Issues Found:
- Substituted capacitors
- Poor solder joint profile
- Firmware test only covered 60% of functions
- No serialization—no field traceability
Action: They transferred to a U.S.-based EMS partner where:
- Functional testing was expanded and automated
- BOM was locked and validated with sourcing oversight
- Serialization was enforced from the first unit
- Root cause process reviews were completed within days
Results:
- Field failure rate dropped from 12% to 0.8%
- RMA costs decreased by 72%
- These improvements highlighted in their Series B investor diligence
What to Ask When Evaluating a Domestic EMS Partner
To ensure your EMS partner is built for quality-first execution, ask:
- Are you certified in ISO 9001, ISO 13485, and ITAR?
- How do you manage and track component substitutions?
- What test coverage and inspection systems are built into your process?
- How is traceability implemented—from BOM to serialized product?
- Do you provide real-time access to yield and failure data?
- Can we collaborate directly with your quality and test engineers?
Final Word: Reshoring Is a Quality Investment
Quality in high-mix electronics depends on performance at shipment and how it holds up in the field, under audit, and across revisions. This is what protects brand equity, accelerates certification, and reduces total cost of ownership.
Reshoring not only provides proximity but also enhances clarity, control, and confidence in the manufacturing operations. Whether you're building MedTech systems under FDA oversight or defense hardware under ITAR constraints, U.S.-based EMS partners like EST are equipped to deliver precision, accountability, and speed—without compromise. This resurgence in domestic manufacturing supports both quality and economic growth.
Key Takeaways
- Offshore quality control obscures yield data, traceability, and risk management
- Reshoring provides visibility, standardized compliance, and test infrastructure
- Domestic EMS partners accelerate iteration, root cause analysis, and audit prep
- High-reliability teams reduce cost by improving quality upstream