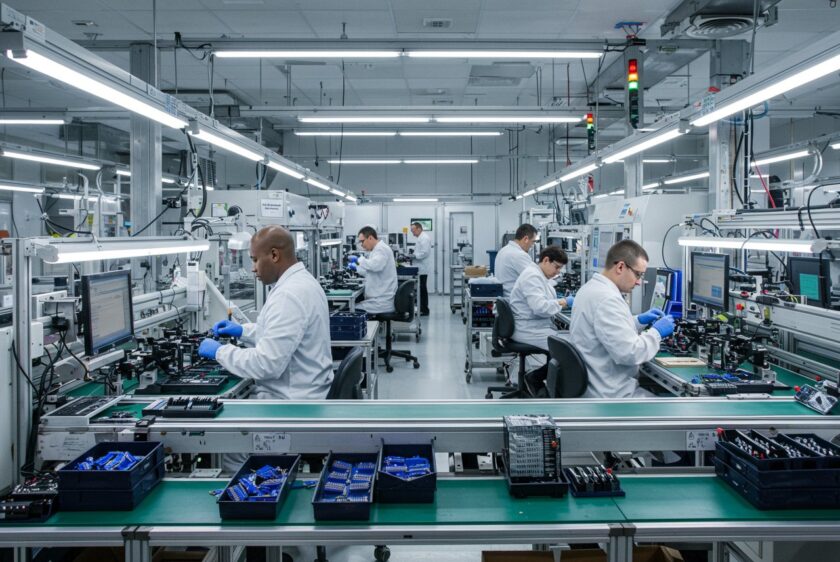
Compliance is how trust gets built into a product
For MedTech and Defense startups, trust is currency. But here’s the problem: too many engineering teams treat compliance like an endpoint. Something that gets “handled later”—after design is locked, after sourcing is done, after builds have started. And by then, it’s too late.
Here’s the truth: if your engineering team isn’t thinking about compliance from day one, you’re already behind.
Compliance: Not just a box to check
Most startups treat compliance like it lives in QA or regulatory. That’s a mistake.
In high-stakes sectors, compliance isn’t just paperwork. It governs how you build, who you can buy from, who can touch your files—and whether you’re allowed to ship.
A design that ignores compliance isn’t incomplete. It’s non-viable.
What’s really at risk?
Failure to design with compliance in mind doesn’t just mean “extra paperwork.” It means:
- Regulatory delays (FDA, FAA, DoD)
- Revalidations and rework
- Lost certifications or failed audits
- Broken supply chains during component reviews
- Legal exposure
- Investor doubt
These are not theoretical risks. They’re career-defining failures. Most of them start with small engineering decisions—an undocumented material change, a supplier without RoHS traceability, or a file shared through the wrong platform.
If you want to compete in a regulated space, your compliance posture is either your launch pad—or your liability.
Core standards every engineer should know
If your team is building anything that might touch a regulated market, these aren’t acronyms to memorize later. They are requirements that inform design decisions now.
- ISO 13485 – The quality system that governs medical devices. Required for FDA market clearance and CE mark in the EU.
- ITAR / EAR – U.S. export control laws that restrict file access, supply chain location, and who can physically touch your product.
- RoHS / REACH – Bans on hazardous substances like lead, cadmium, mercury—and increasingly, PFAS. Noncompliant parts mean your product can’t ship.
- TSCA / PFAS Bans – Emerging U.S. regulations that restrict the use of “forever chemicals” in electronics. These are becoming the next asbestos.
- FDA 21 CFR Part 820 – GMP rules for medical device manufacturing. You’ll need to prove you followed them—through documentation.
These frameworks shape how you source, build, test, and verify. If you design outside them, you design yourself into a corner.
How to engineer with compliance in mind
1. DFM ≠ Just for yield
Design for Manufacturability (DFM) isn’t just about board layout. It’s about buildability inside a controlled, traceable, auditable system.
Designing for compliance means you:
- Avoid last-minute component swaps
- Choose parts with clear material declarations
- Create test points with traceability in mind
- Align with your EMS partner’s process early
Fixing a RoHS violation during validation testing? That’s a $50,000 problem.
Catching it at the prototype stage? That’s just good engineering.
2. Understand your manufacturer’s QMS
Your EMS partner’s quality system isn’t background noise. It’s the system your product will live inside. Component engineers should be involved in this process to ensure alignment.
Ask them:
- Are you ISO 13485 certified?
- Are you ITAR registered?
- Can you show me how you document, trace, and audit?
If they can’t show you their audit trail or revision controls, that’s not a supplier. That’s a risk. Supplier reliability is paramount for maintaining supply chain resilience.
A mature QMS protects your launch date—and your reputation.
3. Vet your supply chain like it’s your IP
Compliance doesn’t end with your files. It goes all the way down to the component level, involving strategic sourcing professionals.
- Does your BOM include restricted substances?
- Can every part be traced to a supplier declaration?
- Are your vendors REACH, RoHS, TSCA, and PFAS compliant?
- Do they disclose lifecycle risks or obsolescence flags?
If not, you don’t have a supply chain. You have a blind spot.
Unvetted substitutions are how compliance failures sneak into builds. Vet your vendors. Document the proof. And never accept a part without a paper trail.
4. Build documentation into the design process
If it’s not documented, it didn’t happen. That’s not regulatory jargon. That’s how audits work.
Get your engineering team, especially electronic component manufacturers, in the habit of:
- Keeping revision histories clean and searchable
- Saving test data in standardized, exportable formats
- Logging supplier declarations as part of BOM management
- Maintaining a live compliance matrix through EVT and DVT
The goal is simple: your design should be able to stand up in an audit—without explanations or excuses.
Tools that make compliance easier (and smarter)
Compliance isn’t just a checklist. It’s a system. The right tools make it repeatable.
ERP + PLM integration
Track revisions, part status, supplier certs, and traceability paths. Your ERP and PLM systems are your documentation backbone.
Compliance databases
Use tools like SiliconExpert or Z2Data to screen your BOM for banned substances, high-risk suppliers, and compliance flags early. This helps manage unforeseen disasters.
Supply chain sustainability platforms
Platforms like Assent or Source Intelligence help track full material disclosures, risk scoring, and global compliance status—at scale. They are crucial for identifying components that could lead to out-of-stock situations.
Manufacturing readiness checklists
Work with your EMS partner to co-develop pre-build checklists aligned with your compliance requirements. This avoids delays, mitigates sourcing risk, and prevents post-build surprises.
The shift: from burden to advantage
Compliance is not a barrier to innovation. It’s a filter for build-ready design. When you embrace it early, you:
- Build faster
- Launch cleaner
- Survive audits
- Qualify for restricted markets
- Avoid investor red flags
- Command higher pricing
It also reduces team friction. Fewer change orders. Less scrambling. More confidence from prototyping to production.
Founders who understand this aren’t afraid of audits. They use compliance to win trust—and win markets.
Bottom line: Your engineers are compliance gatekeepers
Even if regulatory isn’t in their job title, engineers make the decisions that determine audit success—or failure.
By integrating compliance at the design level, you:
- Shorten time to market
- Prevent rework
- Secure supply chains
- Build audit-ready products
- Earn trust before you need it
Effective supply chain management in regulated markets ensures that trust isn’t just a marketing message—it’s a manufacturing strategy.
Call to action
If your product lives in MedTech, Defense, or any high-regulation sector—EST can help you build it right the first time, meeting the highest standards of quality and compliance to ensure customer demand is met with precision and reliability.
Ask us about our Prototype-to-Production Risk Audit.
We’ll walk you through how to align your design, your sourcing, and your compliance documentation—before it costs you in delays, out-of-stock situations, rework, or investor confidence.
[Request a Risk Audit] →
Compliance is how trust gets built into a product.
And for MedTech and Defense startups, trust is currency.
But here’s the problem: too many engineering teams treat compliance like an endpoint. Something that gets “handled later”—after design is locked, after sourcing is done, after builds have started. And by then, it’s too late.
Here’s the truth: if your engineering team isn’t thinking about compliance from day one, you’re already behind.
Compliance: Not Just a Box to Check
Most startups treat compliance like it lives in QA or regulatory. That’s a mistake.
Because in high-stakes sectors, compliance isn’t just paperwork. It governs how you build, who you can buy from, who can touch your files—and whether you’re allowed to ship.
A design that ignores compliance isn’t incomplete.
It’s non-viable.
What’s Really at Risk?
Failure to design with compliance in mind doesn’t just mean “extra paperwork.” It means:
- Regulatory delays (FDA, FAA, DoD)
- Revalidations and rework
- Lost certifications or failed audits
- Broken supply chains during component reviews
- Legal exposure
- Investor doubt
Absolutely, human error plays a significant role in these scenarios. Even the smallest oversight can lead to major compliance and regulatory issues down the line. This is why integrating compliance into every stage of the design and manufacturing process is crucial.
Here's an update to your text reflecting this point:
These are not theoretical risks. They’re career-defining failures. And most of them start with small engineering decisions—an undocumented material change, a supplier without RoHS traceability, a file shared through the wrong platform. Human errors like these can have far-reaching consequences in high-stakes industries.
If you want to compete in a regulated space, your compliance posture is either your launch pad—or your liability.
Core Standards Every Engineer Should Know
If your team is building anything that might touch a regulated market, these aren’t acronyms to memorize later. They are requirements that inform design decisions now.
- ISO 13485 – The quality system that governs medical devices. Required for FDA market clearance and CE mark in the EU.
- ITAR / EAR – U.S. export control laws that restrict file access, supply chain location, and who can physically touch your product.
- RoHS / REACH – Bans on hazardous substances like lead, cadmium, mercury—and increasingly, PFAS. Noncompliant parts mean your product can’t ship.
- TSCA / PFAS Bans – Emerging U.S. regulations that restrict use of “forever chemicals” in electronics. These are becoming the next asbestos.
- FDA 21 CFR Part 820 – GMP rules for medical device manufacturing. You’ll need to prove you followed them—through documentation.
These frameworks shape how you source, build, test, and verify. If you design outside them, you design yourself into a corner.
How to Engineer with Compliance in Mind
1. DFM ≠ Just for Yield
Design for Manufacturability (DFM) isn’t just about board layout. It’s about buildability inside a controlled, traceable, auditable system.
Designing for compliance means you:
- Avoid last-minute component swaps
- Choose parts with clear material declarations
- Create test points with traceability in mind
- Align with your EMS partner’s process early
Fixing a RoHS violation during validation testing? That’s a $50,000 problem.
Catching it at prototype? That’s just good engineering.
2. Understand Your Manufacturer’s QMS
Your EMS partner’s quality system isn’t background noise. It’s the system your product will live inside. Component engineers should be involved in this process to ensure alignment.
Ask them:
- Are you ISO 13485 certified?
- Are you ITAR registered?
- Can you show me how you document, trace, and audit?
If they can’t show you their audit trail or revision controls, that’s not a supplier. That’s a risk. Supplier reliability is paramount for maintaining supply chain resilience.
A mature QMS protects your launch date—and your reputation.
3. Vet Your Supply Chain Like It’s Your IP
Compliance doesn’t end with your files. It goes all the way down to the component level, involving strategic sourcing professionals.
- Does your BOM include restricted substances?
- Can every part be traced to a supplier declaration?
- Are your vendors REACH, RoHS, TSCA, and PFAS compliant?
- Do they disclose lifecycle risks or obsolescence flags?
If not, you don’t have a supply chain. You have a blind spot.
Unvetted substitutions are how compliance failures sneak into builds. Vet your vendors. Document the proof. And never accept a part without a paper trail.
4. Build Documentation into the Design Process
If it’s not documented, it didn’t happen. That’s not regulatory jargon. That’s how audits work.
Get your engineering team, especially electronic component manufacturers, in the habit of:
- Keeping revision histories clean and searchable
- Saving test data in standardized, exportable formats
- Logging supplier declarations as part of BOM management
- Maintaining a live compliance matrix through EVT and DVT
The goal is simple: your design should be able to stand up in an audit—without explanations or excuses.
Tools That Make Compliance Easier (and Smarter)
Compliance isn’t just a checklist. It’s a system. The right tools make it repeatable.
ERP + PLM Integration
Track revisions, part status, supplier certs, and traceability paths. Your ERP and PLM systems are your documentation backbone.
Compliance Databases
Use tools like SiliconExpert or Z2Data to screen your BOM for banned substances, high-risk suppliers, and compliance flags early. This helps manage unforeseen disasters.
Supply Chain Sustainability Platforms
Platforms like Assent or Source Intelligence help track full material disclosures, risk scoring, and global compliance status—at scale. They are crucial for identifying components that could lead to out-of-stock situations.
Manufacturing Readiness Checklists
Work with your EMS partner to co-develop pre-build checklists aligned with your compliance requirements. This avoids delays, mitigates sourcing risk, and prevents post-build surprises.
The Shift: From Burden to Advantage
Compliance is not a barrier to innovation. It’s a filter for build-ready design. When you embrace it early, you:
- Build faster
- Launch cleaner
- Survive audits
- Qualify for restricted markets
- Avoid investor red flags
- Command higher pricing
It also reduces team friction. Fewer change orders. Less scrambling. More confidence from prototyping to production.
Founders who understand this aren’t afraid of audits. They use compliance to win trust—and win markets.
Bottom Line: Your Engineers Are Compliance Gatekeepers
Even if regulatory isn’t in their job title, engineers make the decisions that determine audit success—or failure.
By integrating compliance at the design level, you:
- Shorten time to market
- Prevent rework
- Secure supply chains
- Build audit-ready products
- Earn trust before you need it
Effective supply chain management in regulated markets ensures that trust isn’t just a marketing message—it’s a manufacturing strategy.
Call to Action
If your product lives in MedTech, Defense, or any high-regulation sector—EST can help you build it right the first time.
Ask us about our Prototype-to-Production Risk Audit.
We’ll walk you through how to align your design, your sourcing, and your compliance documentation—before it costs you in delays, out-of-stock situations, rework, or investor confidence.
[Request a Risk Audit] →