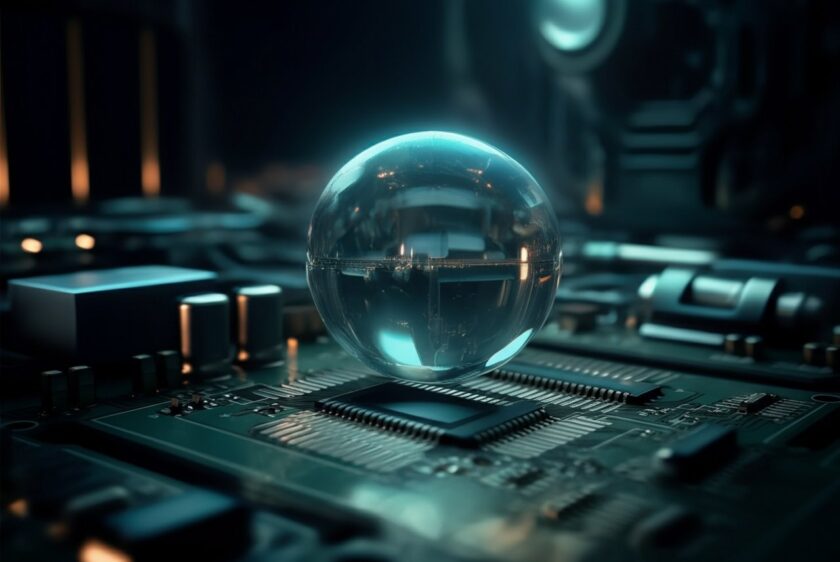
For years, medical device development followed a predictable, modular blueprint:
- Board design by one vendor
- Sourcing by another
- Assembly outsourced elsewhere
- In-house testing (if resources allowed)
- Packaging, labeling, and logistics yet another handoff
Initially, this segmented approach provided flexibility and agility—until the landscape dramatically shifted.
Fragmentation Worked—Until the Stakes Got Higher
The traditional model served well when rapid prototyping, flexibility, and low-volume production dominated the medical device sector. Regulatory oversight was lighter, global supply chains were stable, and investment pressures were less intense.
Today’s reality is vastly different:
- Heightened Regulatory Complexity: FDA, MDR, ISO 13485, UDI, and cybersecurity guidelines require meticulous documentation and compliance.
- Unpredictable Supply Chains: Global disruptions have amplified risks significantly.
- Investor Demands: Pressure for swift risk mitigation and clear scalability paths are intensifying.
- Stringent Traceability: Robust systems for post-market surveillance, product recalls, and field support have become mandatory.
In this environment, fragmented manufacturing is no longer a convenience; it's a vulnerability.
Defining Turnkey EMS
Turnkey EMS providers offer comprehensive manufacturing ecosystems, delivering:
- Strategic component sourcing
- Medical-grade PCBA assembly
- Advanced testing methodologies
- Integrated mechanical assembly (box builds, enclosure assembly)
- Full-scale packaging, labeling, and regulatory compliance
- Complete traceability and serialization
- Lifecycle support, from initial design through commercial launch and beyond
Turnkey EMS isn’t simply outsourcing—it’s partnership and accountability from start to finish.
5 Reasons Medical Device Teams Are Turning to Turnkey EMS
1. Streamlined Design Transfer
The shift from R&D to manufacturing isn’t merely administrative; it's critical to regulatory compliance. Turnkey EMS partners establish robust documentation processes in parallel with initial builds, significantly reducing validation risks, and regulatory hurdles. This ensures all product types meet the necessary standards.
2. Simplified Change Management
Design adjustments in fragmented environments trigger multi-vendor communications, delays, and complex documentation revisions. Turnkey partners centralize these processes, simplifying Engineering Change Orders (ECOs), validations, and documentation updates, thus enhancing adaptability to constant changes.
3. Continuous Regulatory Compliance
Turnkey providers maintain comprehensive Quality Management Systems (QMS), ensuring alignment with regulatory expectations and seamless handling of FDA and MDR submissions, internal audits, and traceability reports. Rigorous quality control mechanisms are embedded in every production method to guarantee high quality finished products.
4. Preemptive Risk Mitigation
Turnkey EMS partners embed systems that proactively address post-market risks, including field failure tracking, recall response, and CAPA management. This ensures preparedness and rapid action when needed. Advanced industrial CT scanning options might also be included to ensure product integrity and support quality assurance.
5. Accelerated Scalability
As market validation occurs, turnkey providers rapidly scale production without sacrificing traceability or quality. Infrastructure is built for growth, streamlining production increases in both small quantities and large quantities without requalification headaches.
Choosing the Right Turnkey EMS Partner
A true turnkey EMS partner will have:
- ✅ ISO 13485 Certification
- ✅ Comprehensive FDA and MDR-aligned documentation
- ✅ Extensive regulatory audit experience
- ✅ Robust DFM and DFT support
- ✅ End-to-end lifecycle traceability
- ✅ Secure file handling
- ✅ Proven processes for scalable production
- ✅ Specialized UDI and labeling expertise
If these criteria aren’t met, you’re engaging in transactional, not strategic, manufacturing.
Why the Shift is Inevitable
Regulatory environments and market pressures increasingly demand:
- Faster, disciplined builds
- Scalability engineered into processes from day one
- Manufacturing integration as part of regulatory strategies
- Strategic vendor consolidation with higher accountability standards
Turnkey EMS addresses these market imperatives by embedding traceability, repeatability, and regulatory rigor into every phase of manufacturing. This holistic approach is essential to cater to diverse customer needs, especially in sectors like aerospace components and medical devices requiring specialized performance components.
Final Thought: Proof is as Important as Production
In medical device manufacturing, how you document your processes is as critical as how you execute them. Turnkey EMS partners provide the transparency, traceability, and regulatory strength required for seamless global launches. Adopting data-driven insights and digital technologies ensures adaptability to market changes and long-term success in make-to-order manufacturing environments.
At EST, our entire operation is crafted around supporting medtech innovators who demand not just manufacturing excellence, but complete lifecycle accountability.
Before selecting a partner, ask yourself:
“Will this partner help us ship faster—or submit cleaner?”
The ideal partner excels at both.