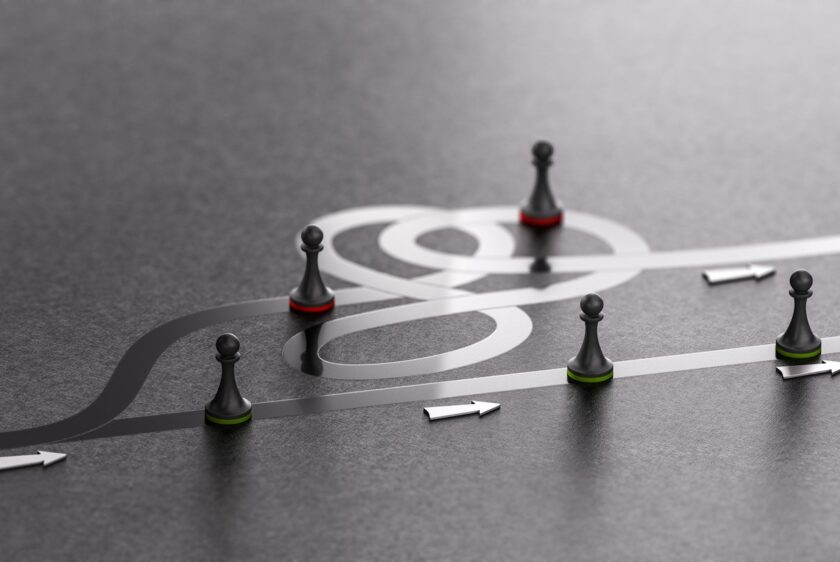
Speed is seductive.
It captures investor interest, earns first-mover advantage, and looks impressive in pitch decks. But in the world of high-reliability electronics—where products control surgical robots, guide flight control systems, and uphold critical infrastructure—speed without resilience becomes a serious liability.
A single failed component, a supplier hiccup, or an unforeseen firmware crash can derail an otherwise groundbreaking product. Successful original equipment manufacturers (OEMs) and startups aren't simply building for speed; they're building for resilience—designing for unexpected failure modes, compliance audits, shifting launch windows, and material shortages from day one.
Here's how you can integrate resilience into your product, processes, and relationships with your electronics manufacturing partner from the outset.
Resilience: A Design Constraint, Not an Afterthought
In many engineering teams, resilience is discussed only after something breaks—a firmware update bricks deployed devices, a sensor fails in extreme conditions, or a unit inexplicably goes offline.
But by then, it's often too late. High-reliability electronics demand resilience as a fundamental design constraint:
- Design for sourcing volatility: What if a key component suddenly becomes unavailable?
- Design for compliance: Can your product seamlessly pass critical certifications like EMC or ISO 13485?
- Design for field recovery: How easily can your system recover from lost communications or power?
- Design for auditability: Can every component and subassembly be traced back to its source?
Addressing these questions upfront prevents reactionary firefighting and promotes proactive risk management.
Why Resilience Matters More for High-Reliability OEMs and Startups
Startups and legacy original equipment manufacturers (OEMs) alike face a shared reality: trust is non-negotiable.
For startups, one failed pilot or product delay due to sourcing issues can devastate investor confidence and market adoption. For established OEMs, even one defective batch can trigger costly recalls and irreparable brand damage.
In today’s turbulent supply chain environment, no one can afford reliance on speed alone. The differentiator is resilience built systematically into every step for long-term success.
5 Principles for Building Resilient Electronics
These proven principles, drawn from EST’s extensive work across critical sectors like medical, aerospace, industrial, and energy, can guide you:
1. Assume the Supply Chain Will Break
- Treat your BOM as a design input, not an afterthought.
- Pre-qualify alternate parts, avoid sole-sourced components, and continuously assess sourcing risks during design reviews.
2. Make Reliability Observable
- Incorporate robust logging, debug ports, self-tests, and structured logs from the prototype stage.
- Transparency in failure can become a competitive advantage, proving reliability through observable performance.
3. Modularize Your Architecture and Processes
- Adopt modular hardware and firmware designs that allow seamless updates and troubleshooting.
- Modular processes streamline validation, testing, and scaling—whether you're reworking prototypes or onboarding new electronics manufacturing services (EMS) partners.
4. Turn Compliance into Competitive Advantage
- Integrate standards such as ISO 13485, IPC-A-610 Class 3, and UL 61010 early.
- Maintain meticulous design history files and rigorous margin validations (thermal, electrical, mechanical).
5. Invest in Informed Speed
- Move quickly through short, validated development loops (EVT, DVT, PVT, pilot).
- Engage your electronics manufacturing partner early, involving them deeply as a strategic ally rather than simply a vendor.
- Document meticulously—future audits and redesigns will become seamless.
Agility for Startups: Build Habits That Scale
Startups can leverage agility to adopt scalable resilience practices and gain a competitive advantage:
- Maintain thorough design histories without bureaucratic complexity.
- Develop testable, structured firmware instead of rapid, fragile fixes.
- Select components available at scale, not merely those with impressive datasheets.
OEMs: Resilience as Innovation
Established OEMs can convert institutional resilience into a strategic asset for business success:
- Ensure resilience practices are documented and teachable.
- Integrate resilience deeply into new product development cycles.
- Combine resilience with agile, responsive systems.
Leading OEMs treat resilience as innovation, making it a key selling point to differentiate their high-reliability products.
What You Build Is Only as Strong as How You Build It
Resilience isn't just a buzzword; it’s a proactive stance ensuring your product reliably meets market demands even when conditions deviate from ideal. In critical sectors, resilience isn’t merely desirable—it is essential for long-term success.
At EST, we've successfully guided clients through complex sourcing emergencies, global shortages, and critical audits by embedding resilience from the earliest design stages. Here, speed becomes a direct result of clarity, not chaos.
TL;DR: Resilient Design, No Slowdowns
- Design for lifecycle resilience, not just launch.
- Treat sourcing, compliance, and auditability as critical design constraints.
- Prioritize visibility in reliability and ease of adaptability.
Because true market leaders in high-reliability electronics don't just reach the market first—they thrive through the challenges the market inevitably presents, building a strong foundation for long-term success.