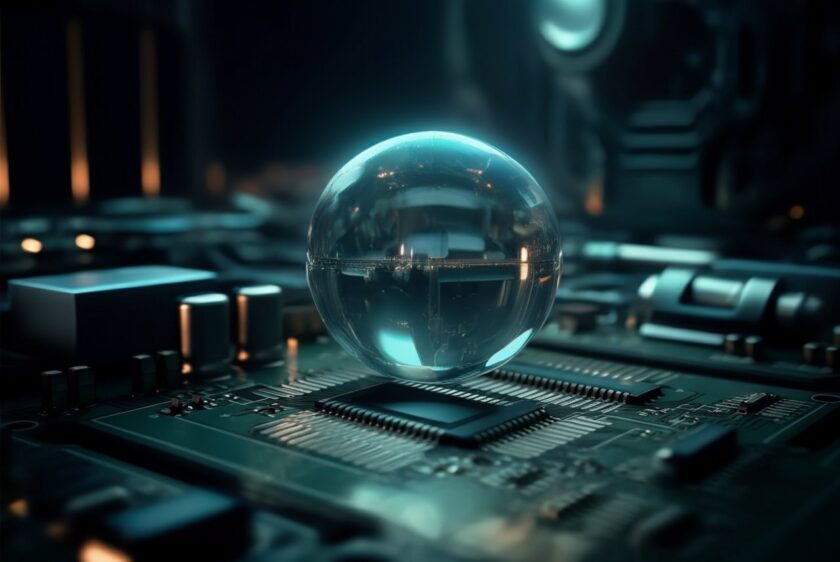
In the realm of military electronics, where precision and reliability are non-negotiable, ensuring signal integrity in high-speed Printed Circuit Board (PCB) designs is paramount. The complexity and stringent requirements associated with these designs necessitate a thorough understanding of various factors that can impact signal performance. This article delves into the critical aspects of maintaining signal integrity in high-speed military PCB designs, offering insights into best practices and advanced techniques.
The Importance of Signal Integrity
Signal integrity refers to the quality and reliability of electrical signals as they travel through a PCB. In military applications, poor signal integrity can lead to data corruption, system failures, and potentially catastrophic consequences. Given the mission-critical nature of military electronics, it is essential to ensure that signals remain clear and undistorted from source to destination.
Factors Affecting Signal Integrity
Several factors can influence signal integrity in high-speed PCB designs:
- Impedance Mismatch: Variations in impedance along the transmission path can cause reflections and signal distortion.
- Crosstalk: Electromagnetic interference between adjacent traces can degrade signal quality.
- Transmission Line Effects: High-frequency signals behave differently than low-frequency ones, requiring careful consideration of transmission line properties.
- Power Supply Noise: Fluctuations in power supply voltage can introduce noise into the system.
Understanding these factors is crucial for designing PCBs that meet the rigorous demands of military applications.
Design Considerations for High-Speed Military PCBs
To ensure optimal signal integrity in high-speed military PCBs, designers must adopt a holistic approach that encompasses layout strategies, material selection, and simulation techniques.
Layout Strategies
The physical layout of a PCB plays a significant role in maintaining signal integrity. Key considerations include:
- Controlled Impedance Traces: Designing traces with controlled impedance helps minimize reflections and ensures consistent signal propagation.
- Proper Trace Spacing: Adequate spacing between traces reduces crosstalk by minimizing electromagnetic coupling.
- Ground Planes: Implementing solid ground planes provides a return path for signals and reduces noise.
- Via Management: Minimizing via usage or using back-drilled vias can reduce parasitic inductance and capacitance.
Material Selection
The choice of materials affects both electrical performance and environmental resilience:
- Low-Loss Dielectrics: Using materials with low dielectric loss minimizes signal attenuation at high frequencies.
- Thermal Stability: Materials should withstand extreme temperatures typical in military environments without degrading performance.
- Mechanical Robustness: Durability against mechanical stress ensures long-term reliability.
Simulation Techniques
Advanced simulation tools enable designers to predict potential issues before fabrication:
- Signal Integrity Analysis Software: Tools like HyperLynx or Ansys SIwave simulate electromagnetic behavior to identify problems such as reflection or crosstalk.
- Electromagnetic Interference (EMI) Modeling: Simulating EMI helps mitigate interference from external sources or adjacent components.
- Power Integrity Analysis: Ensuring stable power delivery through simulations prevents noise-induced errors.
Compliance with Military Standards
Military PCBs must adhere to stringent standards such as MIL-STD-461 for electromagnetic compatibility (EMC) and MIL-PRF-31032 for printed wiring boards' performance specification:
- MIL-STD-461 Compliance: This standard specifies limits on electromagnetic emissions and susceptibility to ensure systems do not interfere with each other or succumb to external interference.
- MIL-PRF-31032 Certification: Ensures that PCBs meet rigorous manufacturing quality requirements necessary for reliable operation under harsh conditions.
Adhering to these standards guarantees that military electronics perform reliably even in challenging environments.
Conclusion: Precision-Built Electronics You Can Trust
At Electro Surface Technologies (EST), we understand the critical importance of ensuring signal integrity in high-speed military PCB designs. Our expertise spans over 35 years of delivering precision-built electronics compliant with ISO 13485, ITAR regulations, and FDA standards—making us your trusted partner for mission-critical applications.
By leveraging advanced design techniques, selecting appropriate materials, utilizing cutting-edge simulation tools, and adhering strictly to military standards—we provide secure U.S.-based manufacturing solutions tailored specifically for defense contractors seeking unparalleled reliability.
Partnering with EST means no compliance failures or offshore risks—just precision-built electronics you can trust when failure is not an option!