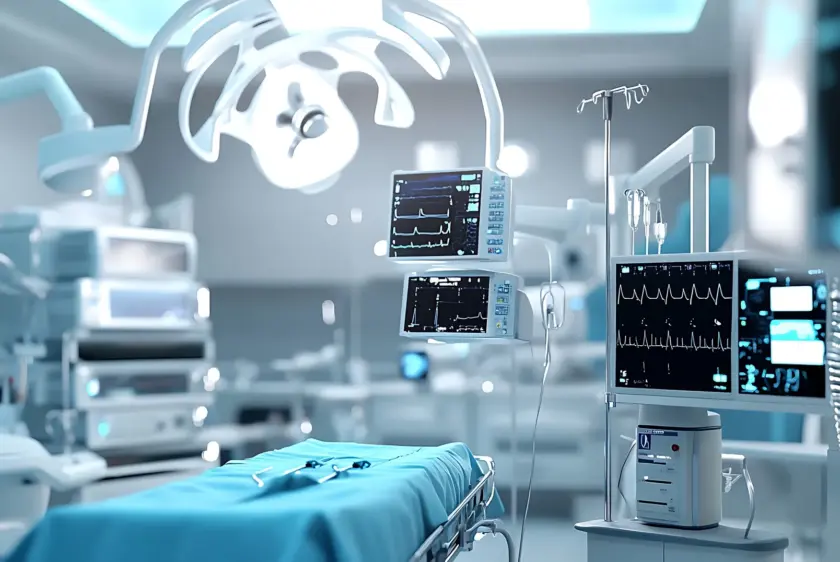
In the medical device industry, speed to market is critical—but cutting corners on FDA compliance during rapid prototyping can lead to regulatory setbacks, costly redesigns, and delayed product launches. Ensuring that your prototyping process aligns with FDA requirements is essential for avoiding compliance pitfalls while maintaining development speed.
This guide explores how FDA-compliant rapid prototyping enables medical device manufacturers to innovate quickly without sacrificing quality, safety, or regulatory adherence.
1. Understanding FDA Compliance in Medical Device Prototyping
What is FDA Compliance?
FDA compliance ensures that medical devices meet stringent regulatory requirements for safety, effectiveness, and quality control. For companies developing medical devices, this means adhering to:
- ✅ ISO 13485 – Quality management systems for medical devices
- ✅ 21 CFR Part 820 – FDA’s Quality System Regulation (QSR)
- ✅ ISO 14971 – Risk management for medical devices
- ✅ Good Manufacturing Practices (GMP) – Ensuring consistent, high-quality production
- ✅ PMA vs. 510(k) Regulatory Pathways – Determining if a device requires Premarket Approval (PMA) for high-risk devices or 510(k) clearance for demonstrating equivalence to an existing product
📌 Why It Matters: Failing to follow these regulations during prototyping can lead to delayed FDA approvals, increased costs, and product recalls.
What is Rapid Prototyping in Medical Devices?
Rapid prototyping is the process of quickly creating functional models or iterations of a medical device to test form, fit, function, and usability before full-scale production. Key benefits include:
- ✅ Faster design iteration & validation
- ✅ Reduced development costs
- ✅ Early-stage regulatory assessments
- ✅ Minimized time-to-market
2. Key Challenges in FDA-Compliant Rapid Prototyping
❌ Material Compliance Issues Many rapid prototyping materials may not meet biocompatibility or sterilization standards required for medical devices.
📌 Solution: Use FDA-approved materials (e.g., USP Class VI plastics, medical-grade silicones) and validate them early in the prototyping phase.
❌ Design Control & Documentation Gaps Rapid prototyping often moves quickly, but failing to document changes and validation steps can lead to regulatory noncompliance.
📌 Solution: Implement a traceable design history file (DHF) and maintain a device master record (DMR) to ensure all iterations are FDA-compliant.
❌ Inadequate Risk Management Prototyping must factor in ISO 14971 risk assessments to ensure patient safety and device efficacy.
📌 Solution: Incorporate Failure Mode and Effects Analysis (FMEA) in the early design stages to mitigate potential risks before FDA submission.
3. Best Practices for FDA-Compliant Rapid Prototyping
✔ Use FDA-Recognized Materials & Processes
- Select biocompatible, sterilizable materials suitable for medical applications.
- Ensure that 3D printing, CNC machining, and injection molding processes align with FDA & GMP standards.
✔ Implement Design Controls from Day One
- Follow ISO 13485-compliant quality management systems.
- Maintain clear documentation in a design history file (DHF).
- Conduct verification & validation (V&V) testing early in development.
✔ Conduct Pre-Submission FDA Engagement
- Engage with the FDA’s Q-Submission (Q-Sub) process for early feedback.
- Perform preclinical testing & usability studies to refine device performance.
✔ Leverage Technology for Compliance & Efficiency
- Digital Twins for Virtual Testing – Simulate device performance before physical prototyping.
- Automated Compliance Documentation – Utilize digital tools to maintain records, design revisions, and testing logs.
- Cloud-Based Collaboration – Secure, real-time document sharing and compliance tracking across teams.
✔ Partner with an FDA-Compliant Manufacturer
- Work with ISO 13485-certified contract manufacturers experienced in rapid prototyping.
- Ensure full traceability, process validation, and risk management support.
4. The EST Advantage: FDA-Compliant Rapid Prototyping
🔹 ISO 13485-Certified Manufacturing We adhere to the highest quality standards for medical device prototyping & production.
🔹 Regulatory-Compliant Materials & Processes All components meet FDA & ISO requirements for safety, sterility, and biocompatibility.
🔹 End-to-End Traceability & Risk Management Our processes ensure full documentation, design control, and compliance tracking.
🔹 Fast-Track FDA Approvals & Market Entry Accelerate time-to-market with compliant rapid prototyping & streamlined regulatory pathways.
Let’s Build FDA-Compliant Prototypes—Faster
If you need rapid prototyping for FDA-regulated medical devices, partner with EST for high-quality, compliance-ready manufacturing.
📞 Call us today at (760) 214-9183
📧 Email us at [email protected]
Speed up innovation without sacrificing compliance. Let’s make it happen.